Polymers: from DNA to rubber ducks
Expert reviewers
Essentials
- Polymers are large molecules made up of long chains or networks of smaller molecules called monomers.
- Natural polymers include silk, hair, proteins and DNA, while synthetic (man-made) polymers include polyethylene, polypropylene and polyester.
- Addition polymerisation is the creation of a polymer by the adding together of monomers in a repeating pattern, with no resulting by-product.
- Varying the molecular structure and length of polymer chains or networks results in different polymers with different properties—such as strength, flexibility, heat resistance and recyclability.
What do DNA, rubber ducks and weird seventies raincoats have in common?
They’re all polymers.
Though you may not realise it, polymers are all around us: not just in our toys, clothing and a multitude of plastic products, but in the things we eat, and even in our bodies. But what are polymers, exactly? Are they the same as plastics? How do you make them? And what do they have to do with paperclips?
What is a polymer?
Polymers are large molecules GLOSSARY moleculesa group of atoms bonded together . They’re made from a number of smaller molecules known as monomers.
One way of thinking about polymers is like a chain of connected-up paperclips.
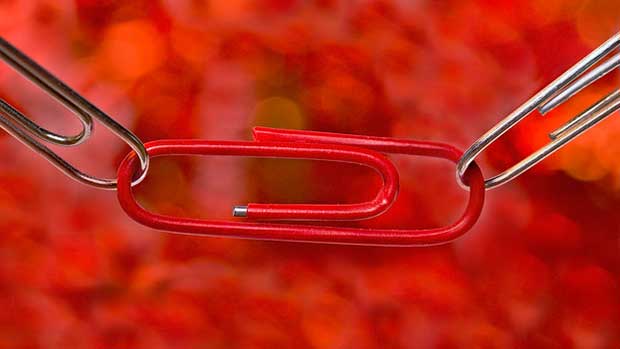
Say you’re feeling creative and decide to make a pattern (one silver, one red, one silver) which you then repeat in a long chain. You might decide to have some extra paperclips branching off your main chain. Or you may think that a paperclip wall-hanging would be a great idea (let’s face it, who wouldn’t?) and join a number of chains together crosswise to make a mat-like network.
Like paperclips, monomers are able to bond together in long chains. These chains can be linear, branched or networked. When you make a paperclip chain, it’s the wire of the joined clips that holds your creation together. Monomers join together to make polymer chains by forming covalent bonds—that is, by sharing electrons. Other bonds then hold the groups of chains together to form a polymer material.
Natural and synthetic polymers
When most people think of polymers, the first things that jump to mind tend to be man made—Aussie banknotes, for instance, or weird seventies PVC raincoats. But there are also many polymers that occur in nature. The starches found in corn and potatoes are polysaccharides (sugar polymers). Silk and hair are polymers known as polypeptides. Cellulose, which makes up the cell wall of plants, is another natural polymer. The proteins we eat, and which we’re made of, are polymers made up of amino acids. And even our DNA is a polymer—it’s made of monomers called nucleotides.
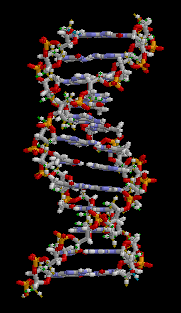
DNA is a naturally occuring polymer. Source: Brian0918 / Wikimedia Commons
The first man-made polymers were actually modified versions of these natural polymers. Celluloid, the stuff from which silent-movie film was made, was a plastic created from chemically modified cellulose. The first completely synthetic polymer (that is, made by people through chemical synthesis), invented in the early years of the twentieth century, was Bakelite: a plastic made by reacting phenol and formaldehyde under pressure at high temperatures. It was discovered when its inventor, Leo Baekeland, was trying to find a replacement for shellac, a natural polymer made from the shells of Asian lac beetles.
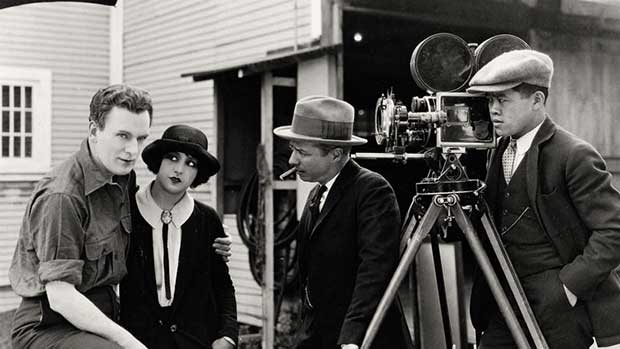
Today, there are all kinds of synthetic polymers, from polyethylene (the world’s most common plastic) to polyester. They’re used to create everything from drainpipes and drink bottles to shrink-wrap and spatulas. Different combinations of monomers in these long polymer chains result in polymers with different properties (more about how and why a bit later on), so polymers can be created depending on what kind of characteristics you need your material to have—strength, durability, flexibility, and so on
Polymers and plastics: what’s the difference?
Although the words ‘polymer’ and ‘plastic’ are often used interchangeably, plastics are actually just one kind of polymer. They’re polymers that have plasticity. In other words, they can be moulded—using heat, for example.
Many plastics are synthesised from hydrocarbon-containing oil or petroleum (though not all plastics are: bioplastics, for example, can be made from plants or even bacteria). The process by which oil is turned into plastic typically goes something like this. First, an oil refinery cracks the oil into small hydrocarbons GLOSSARY hydrocarbons an organic compound made up of only hydrogen and carbon (the monomers). A petrochemical plant receives the monomers and, using the processes which we’ll describe in a moment, these are reacted to become polymers. Finally, the polymers, in the form of a resin (a mass of polymer chains) go to a plastics factory, where additives give the plastic the desired properties. Then it’s moulded or formed into plastic products.
Polymerisation: how polymers are made
The joining up of a long chain of molecules is known as polymerisation.
To keep things simple, let’s look at one kind of polymerisation called ‘addition polymerisation’. In addition polymerisation—you guessed it—monomers are simply added together in a repeating pattern. This results in no other, additional, substance being created.
(The other way in which polymers can be created is called condensation polymerisation. In this process, when each monomer is added to the chain, an additional, small molecule—such as water—is created as a by-product. Nylon and polyester are made this way.)
Addition polymerisation relies on a monomer with a double bond connecting two carbon atoms. A molecule called a free radical is introduced, which causes the double bond to open up and link with the next monomer molecule. The polymer chain forms when the same basic unit is repeated over and over in a regular chain structure. While using free radicals in this way isn’t a new idea, chemists are regularly discovering molecules that are much more efficient at making polymers. This means that polymers can be made faster, cheaper, cleaner and with greater control of the final product.
Let’s zoom in and look at this process in a bit more detail, using the formation of polyethylene as an example.
Polyethylene is the simplest synthetic polymer. It’s made up of just one kind of monomer—ethylene, which is made of two carbon atoms and two hydrogen atoms. (Other polymers can be made of two or more different monomers.) Polyethylene is formed when many thousands of ethylene molecules are joined end to end.
The process kicks off with the heating of a molecule, such as hydrogen peroxide.
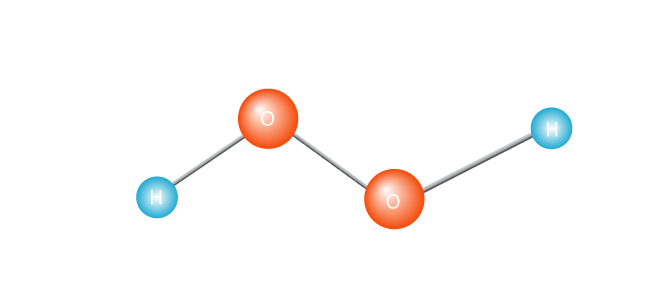
This causes it to cleave in two, creating a free radical. A free radical is a molecule with a single unpaired electron. Electrons are the extroverts of the atom world; they really don’t cope with being alone. Or, to get technical, a molecule with an unpaired electron in its outermost valence shell is an unstable molecule. Either way, the lone electron is going to want to pair up with another electron.
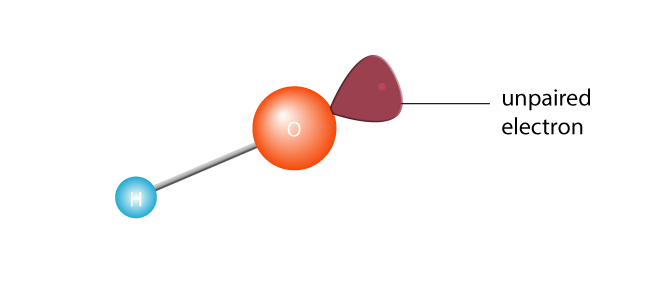
Now we introduce our ethylene molecule.
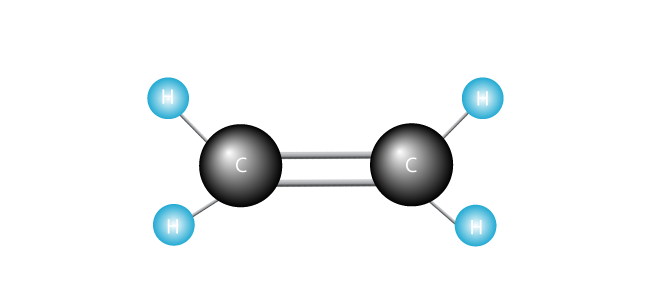
The free radical searches for another electron with which to pair its lonely single electron.
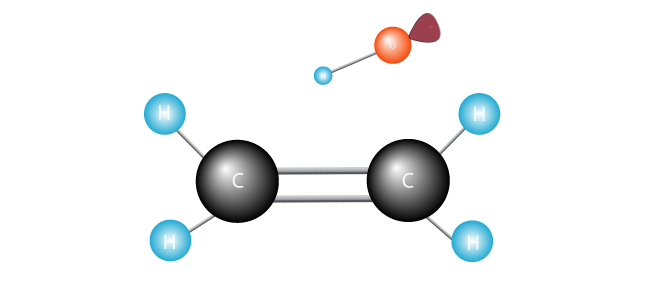
It attacks the double bond joining the two carbons in the ethylene molecule and swipes an electron.
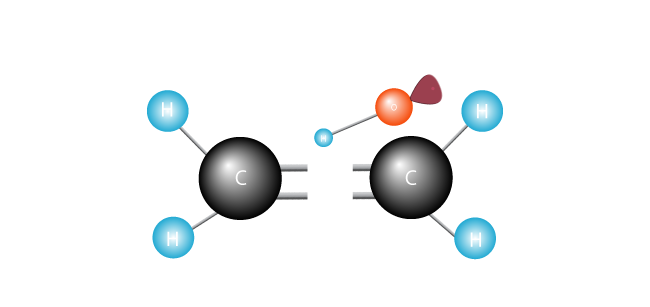
Its electrons happily paired up, the free radical joins one of the carbons.
The other carbon, previously happily paired, now has an unpaired electron. It has become a free radical, with an unpaired electron eager to join up with another to make a pair.
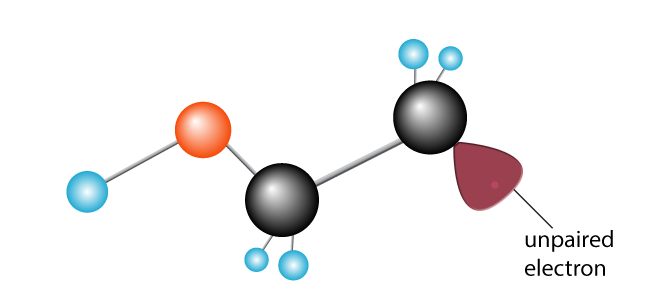
A second ethylene molecule is introduced. The newly created free radical breaks the carbon-to-carbon bond, swiping an electron, and creating a new free radical with a single unpaired electron on the end.
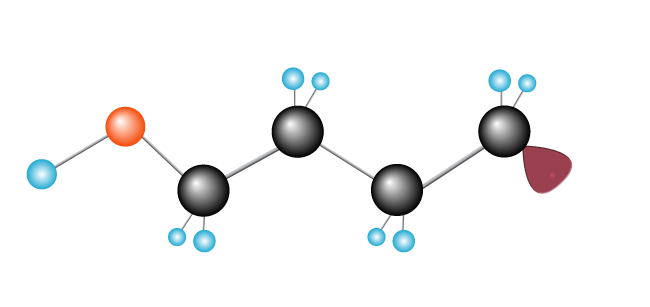
This continues, as a chain reaction, with a long chain forming as more ethylene molecules are added.
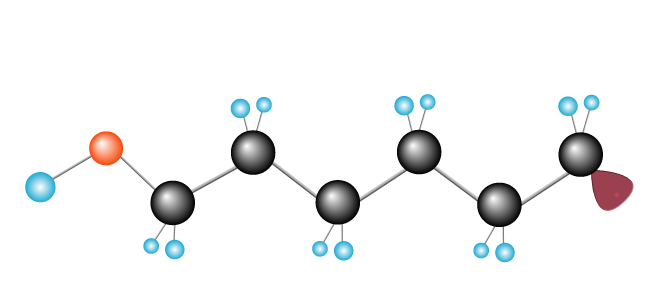
The process keeps going until free radicals meets another free radical, completing the chain.
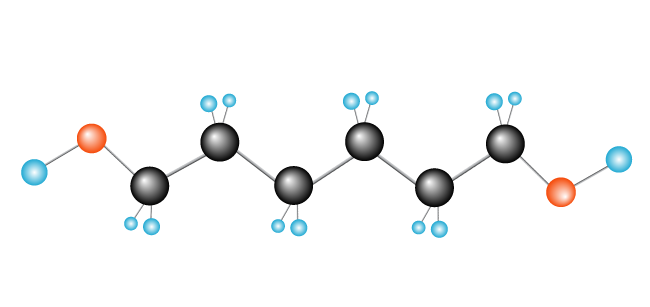
Now we have our polymer, polyethylene, made up of the monomer (repeating unit) ethylene.
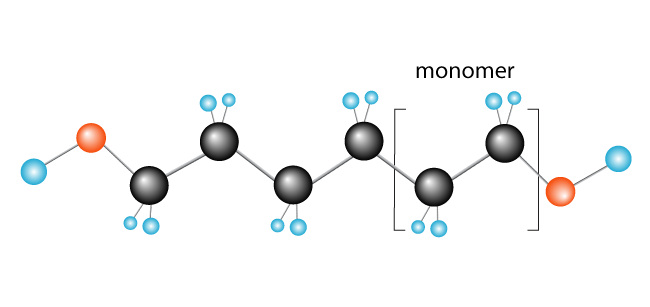
Some other examples of polymers formed in this way are polychloroethylene (PVC), used to make things like plumbing pipes and insulation for electrical cables, and polypropylene, used in products such as rubber ducks (and other toys) and, when processed into fibres, carpets.
Different polymers for different properties
The way molecules are arranged gives different polymers different properties. By manipulating the molecular arrangement, different polymers can be created—depending on whether you want a material that’s strong, stretchy, recyclable or whatever.
Polyethylene, for example, has long polymer chains side by side. They’re often described as being like spaghetti: when heated, they can uncoil and slide easily past each other, giving a material that’s flexible. When they cool down, the chains interact and become entangled. Polyethylene can be melted and reformed into a new shape over and over again. These meltable, reshapable polymers are known as thermoplastics. Other examples include polystyrene and polypropylene.
The strength of polymers also varies depending on how the molecules are arranged. To use our paperclip analogy, you may decide to have some paperclips branching off your main line. This may look pretty funky but, should you decide to turn it into a wall hanging, it’s going to be hard to join it up with another chain in a regular linking pattern. Like your funky side-branching paperclip creation, polymer chains with side branches can’t line up together in a regular pattern. They result in a polymer with a lower density. Low-density polyethylene (LDPE)—the squishy material that plastic bags and wrap (like the kind you might wrap your sandwich in)—is an example. By contrast, polymer chains that don’t have side branches can line up to form a regular (crystalline) structure. The resulting polymer is stronger and has a higher density. An example is high-density polyethylene (HDPE), used to make things like plastic bottles, food containers and plumbing pipes.
In contrast to thermoplastic polymers are thermosetting polymers. These don’t soften when heated and once set into shape are pretty much going to stay that way. That’s because the polymer chains are strongly cross linked in networks. That’s not going to help you much if you want something soft and pliable in which to wrap your sandwich. It is useful, though, for things like car tyres, since a tyre that melts in the heat is going to make for a pretty interesting drive to the beach. Glues and electrical components are also thermosetting polymers.
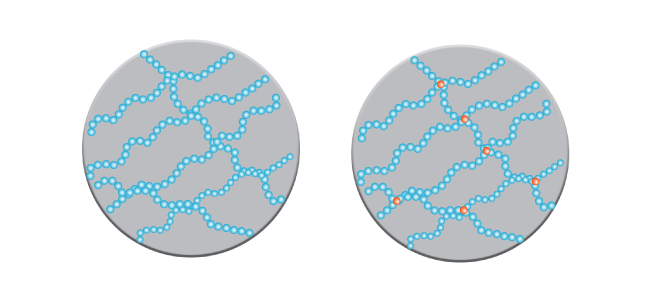
As well as the arrangement of molecules, the properties of a polymer are also determined by the length of the molecular chain. In a nutshell, longer equals stronger. This is because, as a molecule gets longer, the total binding forces between molecules are greater, making the polymer chain stronger. When more than a thousand carbon atoms line up in a chain of ethylene monomers, for example, the resulting polymer, polyethylene, is strong and flexible.
VR contact lenses and printable solar
Developments in synthetic polymers go way beyond plastic bags and drink bottles. Flexible, electricity-conducting polymers may be the next big thing. Into virtual reality (VR)? In the not-too-distant future, you might be able to ditch the chunky goggles and pop in a pair of contact lenses instead, thanks to very thin, electricity-conducting polymer coatings. Australian scientists have also been working on lightweight, flexible solar cells which can be cheaply printed with polymer inks using a conventional printer. Cities of the future could see a multitude of surfaces—buildings, cars, even clothing—made of this power-generating material. Thanks to a plethora of cheap, disposable products and packaging, plastics often get a bad rap (pardon the pun) for their impact on the environment—and rightly so. But new discoveries in materials science—from solar cells to biodegradable plastics made of natural materials—also hold out the promise of a more sustainable future.