Types of batteries
Expert reviewers
Essentials
- There is a huge range of different battery types.
- Different battery chemistries result in batteries that are better suited to certain applications.
- While alkaline batteries account for the bulk of batteries made today, their place at the top will soon be contested by lithium-ion batteries.
- Battery technology will be indispensable in the future as we look for ways store excess electricity generated from wind and solar sources.
Batteries power much of our lives. They’re behind our personal electronics—phones, laptops and hearing aids—our cars, and our power tools. But they’re also essential for the large-scale storage of electricity to support the grid, and for storing the power generated by renewable sources. So many different purposes—they obviously don’t all use the same kind of battery! This has given rise to the development of a huge number of different types of batteries. Here are some of the most common types, how they work, and what they’re good for.
Our old friends
Lead-acid
When was the last time you had to pull out your crank handle, insert it into your car’s crankshaft and give it a good turn to get the engine running? Never? That’s because we have lead-acid batteries connected to our car engines that provide that burst of power the engine needs to get going. These were invented by Gaston Planté in 1859.
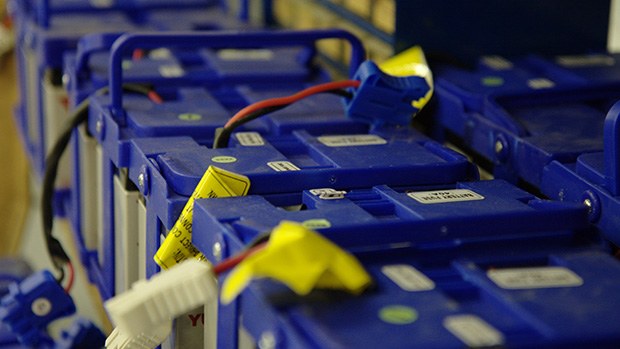
As the name implies, these batteries have some lead in them. In fact, both electrodes (the conductors through which electricity enters or leaves the battery) contain some lead—the anode (positively changed electrode) is made of lead metal (Pb) and the cathode (the negatively charged electrode) is lead dioxide (PbO2). The electrodes are placed within an electrolyte solution of sulphuric acid (H2SO4), which is made up of hydrogen ions (H+) and bisulphate ions (HSO4).
The lead at the anode reacts with the bisulphate from the electrolyte, freeing up some electrons, and producing lead sulphate, which forms crystals upon the anode, and hydrogen ions which go into the electrolyte. The electrons travel over to the cathode via an external circuit, where they, along with bisulphate and hydrogen ions from the electrolyte, react with the lead dioxide cathode. This also produces lead sulphate, which again forms crystals, this time on the cathode.
Lead-acid batteries are rechargeable—the ones in our cars charge up using a little generator connected to the engine, called the alternator. That’s why when you’ve left your car lights on and the battery’s gone flat it’s advisable to drive around for a while after getting the jump-start to give the battery time to charge up again.
As the battery charges, the chemical reactions described above that produce the electricity are forced backwards. The lead sulphate coatings are dissolved and forced back into the electrolyte as Pb2+ and SO42- ions. The Pb2+ ions then pick up two electrons and are re-plated onto the anode as neutral Pb.
At the cathode, the Pb2+ ions give up two electrons to form and react with water (H2O) molecules to re-form neutral lead dioxide on the cathode, and some bisulphate ions that go back into the electrolyte solution.
However, if a lead-acid battery is allowed to discharge too much, or is left too long before recharging, the coatings of lead sulphate form into hard crystals that can’t be removed by the charging process.
Ultrabattery
Developed at CSIRO, the Ultrabattery is a souped-up version of a traditional lead-acid battery. It combines the standard lead-acid battery technology with a supercapacitor. When a normal lead-acid battery discharges, the reaction that drives it results in the formation of lead sulphate crystals on both the anode and cathode. The recharging process removes these coatings, but the electrodes (and therefore the battery) degrade over time. Also, the battery doesn’t like to operate in a partial state of charge—a condition where the battery is subjected to repeated short cycles of discharge and recharge, without ever fully emptying the battery or fully charging it up. This partial state of charge operation is particularly important for vehicles.
The UltraBattery uses the supercapacitor to compensate for the problematic reactions of the lead electrodes in the lead-acid battery, increasing its life span. Because a supercapacitor can take in and store charge very quickly, it can gobble up available power and then feed it to the battery at just the right rate. It manages to reduce the build-up of sulphates that result from the discharge–recharge process in a standard lead-acid battery.
The UltraBattery is also comparatively cheap to make, around 70 per cent cheaper than the lithium-ion batteries currently used in hybrid electric cars. Another potential use for the UltraBattery would be at power stations, to store and ‘smooth’ the energy produced by renewable sources like solar and wind. In large-scale wind farm trials in Australia, the UltraBattery has outperformed conventional lead-acid batteries.
Nickel-cadmium
Although they’re now distinctly old news, nickel-cadmium (NiCad) batteries were the first rechargeable batteries used in power tools, torches and other portable devices. These were the guys in our mobile phones before lithium-ion batteries booted them out. Sometimes they’re still found as old rechargeable AA batteries for torches and toys. Like the lead-acid battery, this cell chemistry has been around for a long time—the first NiCad batteries went on sale in 1910!
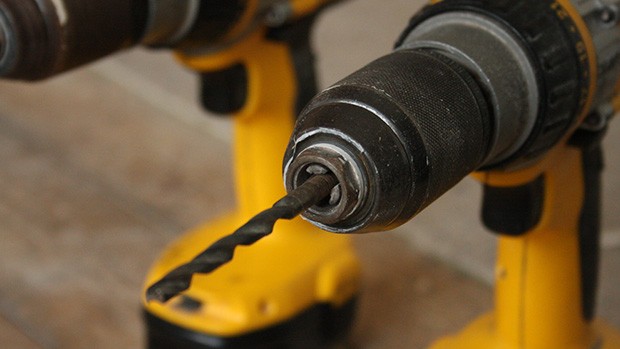
The anode is made from cadmium (Cd) and their cathodes are nickel oxide hydroxide (NiO(OH)2), usually with an electrolyte of potassium hydroxide (KOH).
Nickel oxide hydroxide makes a very good electrode, as it can be produced to have a large surface area, and this increases the active area available for the reaction. Also, it doesn’t react with the electrolyte during the reaction, which keeps the electrolyte solution nice and pure and helps the cell last a (relatively) long time before pesky side-reactions make it degrade.
NiCad batteries had a few shortcomings. Firstly, they were prone to something called the ‘memory effect’, where the batteries would ‘remember’ previous discharge levels and not recharge properly. This was caused by the formation of large, rather than small, cadmium crystals during the recharging process. Ensuring the battery was properly discharged before recharging it went some way towards preventing this problem. But you had to be careful—completely discharging a NiCad battery also damaged it.
Secondly, the self-discharge rate of a NiCad battery is around 15–20 per cent per month. This means that if they sat around on the shelf for a few months, they lost much of their charge.
Thirdly, cadmium is expensive, and a toxic heavy metal, which meant that disposal of the batteries was not a good thing for the environment.
Nickel-metal hydride (NiMH)
These problems with NiCad batteries led to the cadmium anode being replaced with a hydrogen-absorbing intermetallic alloy (a combination of metals with a defined crystal structure) that can gobble up to 7 per cent hydrogen by weight. Essentially, the anode is the hydrogen; the metal alloy merely serves as a storage vessel for it.
The most common combination of metals for this alloy are ones with a strong hydride-forming capability, along with a weak hydride-forming metal.
Another consideration when putting together the metal alloy is that when some metals absorb hydrogen, the reaction gives off heat—it’s exothermic. Others absorb heat in an endothermic reaction. We don’t really want a battery that either produces or sucks in heat as it discharges, so, along with the strong–weak hydride forming combination the alloy is also made from, we need a combination of exothermic and endothermic metals.
Most commonly, the electrode will be a combination of a rare earth element such as lanthanum (La), cerium (Ce) neodymium (Nd) or praseodymium (Pr), mixed with nickel (Ni), cobalt (Co), manganese (Mn) or aluminium (Al).
The electrons that produce the battery’s electric current come from the oxidation of hydrogen atoms, which turn into protons. These protons react with hydroxide ions (OH-) from the electrolyte to make water. The metal alloy that forms the anode along with the hydrogen does not take part in the chemical reaction that drives the cell; it’s basically a bystander that just provides a home for the all-important hydride ions.
Nickel-metal hydride batteries are very similar to NiCad batteries in terms of voltage, capacity and application. The memory effect is less of a problem than with NiCads and they have a higher energy density. They’re still used as the standard for rechargeable AA batteries.
Alkaline
Alkaline batteries are used in toys, electronics, the portable CD players we used in the nineties, and the Walkmans which were popular in the eighties. They account for the bulk of batteries that are made today, although their place at the top will likely soon be contested by the lithium-ion batteries in our phones, laptops and an increasing number of other gadgets.
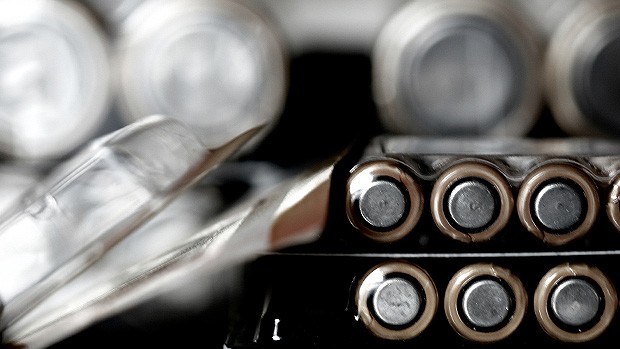
They’re popular because they have a low self-discharge rate, giving them a long shelf life, and don’t contain toxic heavy metals like lead or cadmium. Although rechargeable alkaline batteries have been developed, these guys are generally single use only. Once they’re out of charge, it’s off to the recycling depot (or, more usually, to landfill, as there are not many places that recycle them).
These batteries have zinc as their anode, and manganese dioxide (MnO2) as their cathode. Their name, however, comes from the alkaline solution used as the electrolyte. It’s usually potassium hydroxide (KOH), which can contain a large number of dissolved ions. The more ions the electrolyte solution can absorb, the longer the redox reaction that drives the battery can keep going.
The zinc anode is usually in powdered form. This gives it a greater surface area for reaction, which means the cell can release its power quite quickly. It gives up its electrons to the manganese dioxide cathode, to which carbon, in the form of graphite, is added to improve its conductivity and help it keep its shape.
And this brings us to the batteries that these days power most of our smart phones and laptops: lithium-ion batteries. These guys are so important that we wanted to treat them with the respect (and detail) they deserve, so you can read about them in their very own Nova feature.
The newbies
Redox flow
A redox flow battery does away with reactive electrodes and uses the electrolyte solution to transfer the electrons that create the current. The flow battery still has an anode side and a cathode side but, instead of the metal electrodes that give up and accept electrons, it has two ‘tanks’ full of electrolyte solutions, where the active chemicals are dissolved. There are two types of solution: the anolyte, which replaces the anode of a typical cell, and the catholyte, which acts as the cathode. These solutions are pumped around the battery, and meet in the reaction cell, or ‘stack’. Here, they are separated by a membrane so they don’t mix—ions and electrons, though, can be exchanged through the barrier. They also meet up with the electrodes.
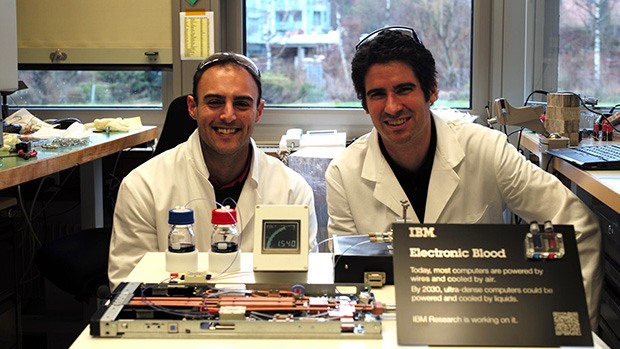
As the anolyte solution contains chemicals of a higher chemical potential than those within the catholyte solution, when the two solutions meet in the reaction cell, electrons from the anolyte are sent through the ion-permeable membrane to the catholyte. These electrons are intercepted and sent off to do their useful work.
Again, it’s a redox reaction that governs the generation of electric current in this type of battery. The anolyte is oxidised when it loses electrons and the catholyte is reduced when it accepts electrons. When all the anolyte has been oxidised, that is, lost all the electrons it had to give, its capacity is spent and it must be recharged.
One good thing about redox flow batteries is that their capacity depends on the size of the tanks of electrolyte solution—if you want a battery that can go for longer, you just need to get bigger tanks, with more solution in them. However, this also means that they’re pretty bulky. Their main use is for industrial-scale operations, like storing the energy produced at wind or solar farms. Your laptop will never contain a flow battery.
The other really neat thing about flow batteries is that, because they don’t have solid electrodes, they don’t suffer from most of the ways that rechargeable batteries degrade over time. In principle, this gives them very long useful lives—perfect for those solar or wind farm uses in which batteries are charged and discharged at least every day.
Flow batteries most commonly use vanadium (V). As this element can happily exist in several different oxidation states—states with different chemical/redox potentials—both the anolyte and catholyte can be made from different forms of vanadium. This solves any problems of cross-contamination between electrolyte solutions made of different elements.
To recharge a flow battery, the system works in reverse. An external voltage is applied, and the electrons that ended up in the catholyte as the battery was used are pushed back into the anolyte, with the positive ions being shoved back into the catholyte.
New research has produced a flow battery that uses lithium ions, and basically works on the same chemistry that underpins the lithium-ion batteries in our phones and laptops. The battery has an anolyte of titanium dioxide (TiO2) and a catholyte of lithium iron phosphate (LiFePO4). Previously, problems with the membrane that separates the two electrolyte solutions have prevented lithium-ion technology being applied successfully in a flow-battery context—they’ve either been too brittle, or haven’t allowed the efficient flow of lithium-ions.
This battery offers a potential energy density 10 times greater than other flow batteries. The rate at which it currently supplies energy is too low for practical use, however, so researchers are looking at ways to improve this.
The major drawback of flow batteries is that their operation depends on a pumping system to circulate the anolyte and catholyte solutions though the reaction cell. This introduces a number of moving parts which must be maintained and serviced regularly.
Lithium-sulphur
Lithium-sulphur batteries promise to be a cheap alternative to pricey lithium-ion options. Sulphur is cheap, and abundant.
The anode of a lithium-sulphur battery would be an extremely thin (and light) sliver of lithium metal. The cathode would be … you guessed it … sulphur (well, a mixture of sulphur and carbon). This combination has a very good potential voltage, and both electrodes would be lighter than those found in conventional lithium-ion batteries, making the battery’s energy density up to five times greater.
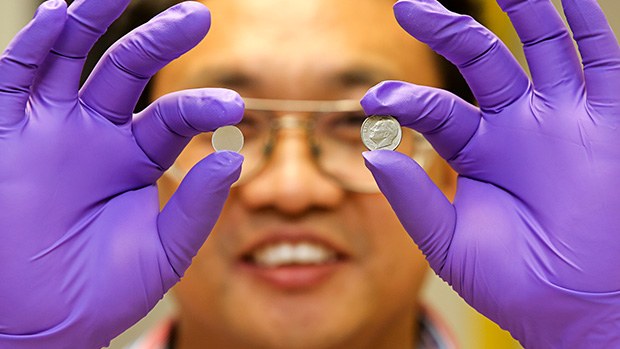
The reaction occurring during discharge involves the oxidation of lithium at the anode, and formation of lithium sulphide. At the same time, electrons are released, providing the electric current. At the cathode, sulphur is reduced and also reacts with lithium, forming a sequential range of compounds with varying amounts of sulphur in them (polysulphides).
$$\text{S}_8 \to \text{Li}_2\text{S}_8 \to \text{Li}_2\text{S}_6 \to \text{Li}_2\text{S}_4 \to \text{Li}_2\text{S}_2$$
The problem is that this battery doesn’t last very long, as the sulphur cathode is not very long lived. Many of the polysulphides dissolve easily within the electrolyte solution, which means that, during each discharge cycle, some of the sulphur from the cathode is irretrievably lost into the solution.
Another issue is that, as lithium reacts with the sulphur of the cathode, the volume of the lithium sulphur compound created is around 80 per cent greater than that of the sulphur cathode before the reaction. This expansion causes the cathode to deteriorate.
Whatever their composition, batteries are indispensable to our everyday lives, and are going to remain so in the future. They will be crucial for powering the ongoing advances in portable technology, enabling the improvement and practicality of electric vehicles, and providing what’s often described as the ‘missing link’ of renewable energy—the ability to store excess electricity generated from wind, solar and other sources for later use.