The mind-bending future of flexible electronics
Expert reviewers
Associate Professor Madhu Bhaskaran
Functional Materials and Microsystems Research Group
RMIT University
Professor Andrew Holmes AC PresAA FRS FTSE
School of ChemistryBio21 Institute
The University of Melbourne
Essentials
- Developments in thin, light and flexible electronics are behind a raft of new innovations, from curved TVs to glucose-monitoring contact lenses.
- The discovery that polymers can be semiconductors has led to the development of printable solar cells and flexible screens using organic light-emitting diodes.
- Biocompatible electronic devices that can flex and stretch have a range of potential medical and health-monitoring uses.
Imagine a paper-thin phone that you could fold up and slip into your wallet. A city in which every surface was generating solar power. Or a wearable ‘smart’ skin that could stop you from getting sick. Flexible electronics could, in the not-too-distant-future, make these incredible ideas a reality.
Printable solar
What if, instead of attaching solar panels to your roof, they were built into the fabric of your curtains, or laminated onto your window panes? Or, instead of plugging in your laptop to recharge the battery, you could charge it on the go, via solar power-generating clothes?
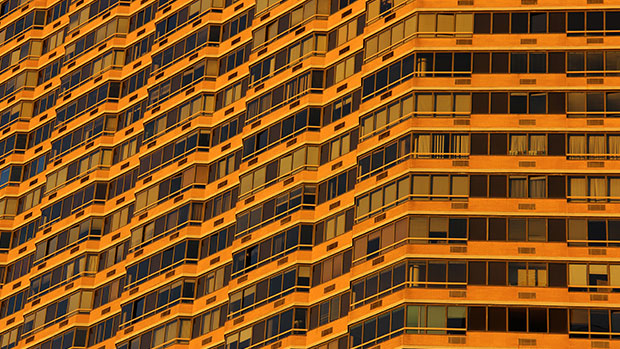
You could, thanks to organic photovoltaics, or OPVs—a thin, flexible alternative to conventional, silicon-based solar panels. Organic photovoltaic cells are made of a ‘sandwich’ of different layers laid down onto a flexible substrate such as plastic. A special kind of polymer called a conjugated polymer is mixed with a substance known as a fullerene (sometimes called a bucky-ball) to create an active layer. A thin film of this blend goes between two electrodes, one of which is transparent. When sunlight is absorbed by the conjugated polymer, the energy can transfer an electron from the polymer to the fullerene. This makes charge flow through the cell, establishing a voltage between the two electrodes.
Solar panels which use an organic, polymer-based layer as the semiconductor have the potential to be a much cheaper alternative to those which use traditional, and expensive, semiconducting materials such as silicon. Not only are polymers cheaper, but they’re thin, light and flexible. The Victorian Organic Solar Cell Consortium, a collaboration between the University of Melbourne, Monash University and CSIRO with a number of industrial partners, has been working on developing a flexible, polymer-based solar cell that can be printed using an ordinary printer.
The process is similar to that used in the production of polymer banknotes, another Australian innovation. It begins with a paper-thin plastic substrate. Initial layers are successively laid down using roll-to-roll printing, then a semiconducting polymer ink is printed on, using a screen printer of the kind commonly used to print designs onto T-shirts. The finished product is about the thickness of an empty chip packet. Its lightness and flexibility means it could, in future, be integrated into curtains to generate power for your home. In developing countries, flexible solar cells could be rolled out onto thatched rooves to provide an alternative to kerosene as a source of power, or keep medicines cool by generating electricity for refrigeration.
After beginning with small (10 x 10 square centimetre) printed panels, the consortium has recently printed A3-sized polymer solar cell modules using this technique. Because they’re based on plastic, and able to be printed on conventional printers, the cells can be produced very quickly and at a low cost. It may be up to a decade before we see them on the market though: while the small, lab-produced cells are as efficient at converting the energy from sunlight to electrcity as silicon solar cells (over 20 per cent efficiency compared with around 18 per cent for commercial silicon panels), a challenge is to make them on the larger scale needed for use in building materials—especially as extremely thin layers need to be precisely laid down, with no pinholes or other imperfections, for the panels to work properly. Making them durable is another issue, as plastics are susceptible to degradation, especially when exposed to moisture. You’ll most likely see early versions of the flexible panels on small items such as backpacks for charging laptops and other devices.
Foldable phones and roll-up TVs
Organic light-emitting polymers, or OLEDs, are another innovation with flexible potential—one that’s already commonly used in our electronic devices.
Like the discovery that plastics can conduct electricity, the finding that polymers can emit light was an accidental discovery. Trying to work out if conjugated polymers could be used as resistors, researchers at Cambridge University in the 1990s sandwiched a thin-film polymer between electrodes and hooked it up to a battery. They were surprised to see the polymer fluoresce (produce a green light)—it was the first time anything like this had ever been seen. Over the following years, they experimented with methods for producing different coloured emissions with polymers. By using an inkjet printer, small dots of these fluorescing polymers could be printed onto a thin, flexible surface to give a full-colour, pixellated flat-screen display.
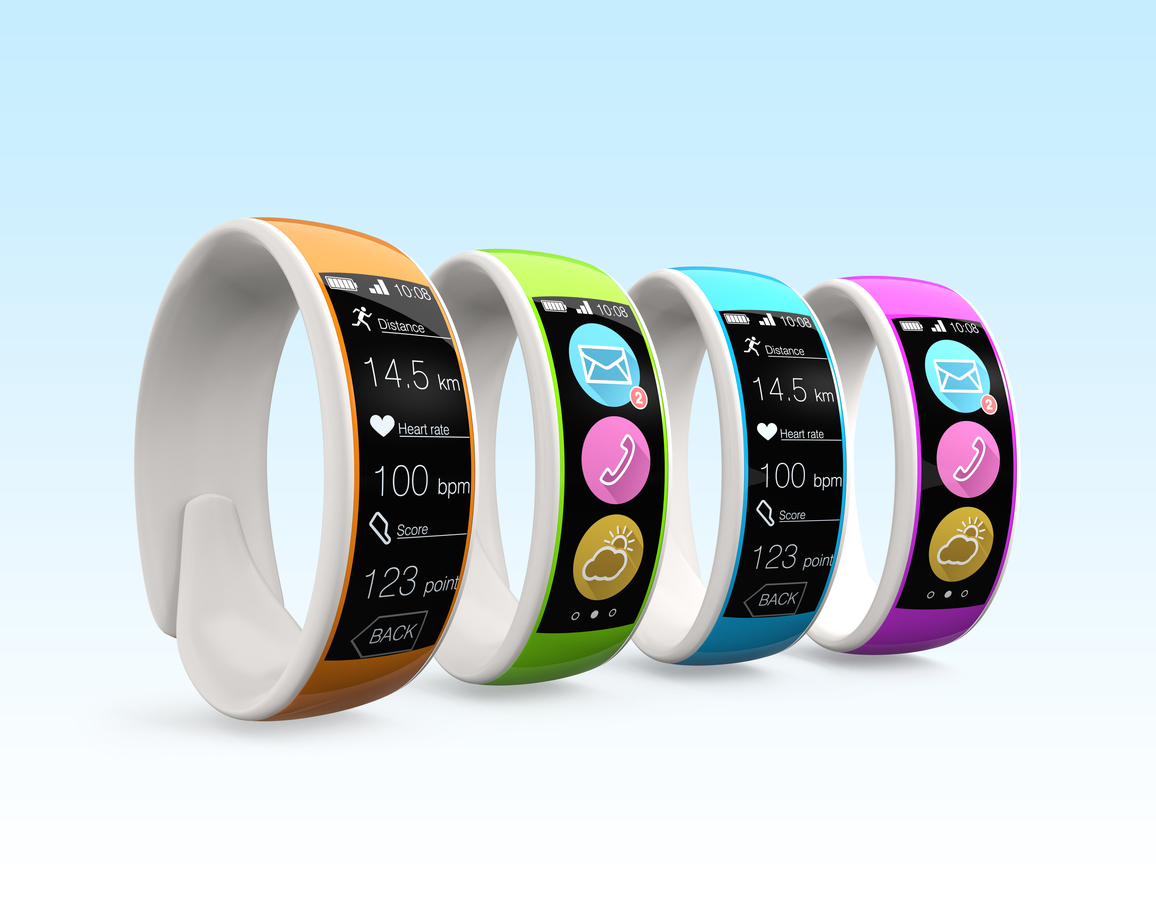
Today, the majority of organic light-emitting diodes—such as the ones found in many smartphone screens and, to a lesser extent, in the displays of some TVs—are based on small molecules rather than polymers (large molecules). Instead of being printed onto a surface, these small, light-emitting molecules are laid down by a process called thermal evaporation, in which a substance is heated up and the resulting vapour adheres to the substrate as a thin film.
In contrast to traditional liquid crystal displays (LCDs), OLEDs don’t need a back light, making them thinner—usually around a tenth of the thickness of LCDs—and more efficient. Because they’re thinner, they’re also more flexible, which means that we could one day see them used in slim, flexible, and even transparent electronic devices like foldable phones or roll-up TVs. We’re not there yet, though—for the moment, OLED TVs are much more expensive to produce and buy than those using LCD displays.
Beyond our personal and entertainment devices, OLEDs have applications in new kinds of lighting. Large areas of light using conventional LEDs are achieved through using banks of many single lights. By contrast, OLEDs can emit uniform and diffuse light across one large surface.
Smart windows
Sometimes we don’t want to emit light, but block it—creating some cool, indoor shade on a bright summer’s day, for example. Smart windows, also known as electrochromic glass, allow us to switch from transparent to dark to block out light.
The basic concept is that, by applying an electric voltage, you can change a material’s colour. Electrochromic glass is already in use in the dimming windows on the Dreamliner 787 aeroplane, and in the rear-view mirrors in some luxury cars. Generally, the colour changing material needs to be in contact with an electrolyte (think salty water). The voltage causes the cations (positively charged ions) or anions (atoms with a negative charge) in the electrolyte to move in or out of the material, inducing the colour change.
Almost all semiconducting and conducting polymers show this ability to change colour—as well as being lightweight and flexible. And, as we’ve seen, by changing the polymer, the resulting colour can also be changed. Electrochromic polymers actually switch colour faster than other materials, and show behaviour called optical memory, which results in much lower power consumption. This means that the smart windows of the future may not only be flexible and come in different colours, but will also consume less energy. The possible uses for electrochromic polymers, however, go beyond a dimmable window in a car or aeroplane; researchers at the University of South Australia are currently developing technology that could enable a military vehicle to change its camouflage at the flick of a switch.
Robot skin and e-lenses
Glucose-checking tattoos for diabetics, stick-on patches for monitoring the vital signs of newborn babies, sensors that can track electrical signals in the brain … thanks to advances in flexible, stretchable electronics, these are some of the possibilities that may be just around the corner.
Because human skin is flexible and stretchy, health-monitoring devices need to be able to bend, flex and stretch too—which is why so much of the work in flexible electronics is in the area of health and medicine. Japanese researchers, for example, have created an electronic ‘skin’ which incorporates organic circuits printed onto plastic film. The material acts as an early warning system for potential health problems such as the onset of infection by monitoring the wearer’s temperature, as well as their pulse and the concentration of oxygen in the blood.
In Australia, scientists at the Functional Materials and Microsystems Research Group at RMIT University in Melbourne have developed a thin, transparent, stick-on patch, similar to a nicotine patch, that can be worn on the skin to track harmful levels of UV radiation known to cause melanoma. Silicone rubber (of the kind that contact lenses are made from) is coated with a layer of zinc oxide a thousand times thinner than a human hair. To enable the patch to be stretchable for use on skin, researchers developed a special transfer process in which the zinc oxide is laid down in a structure much like the Earth’s tectonic plates (but on a much smaller scale), allowing the plates to slide around and over each other. When exposed to harmful levels of UV light, the zinc oxide changes its properties. At the moment, this change is measured by a machine in the lab, but the idea is that, ultimately, the information would be sent wirelessly to your smartphone, sending you a warning when UV levels are high. Such a device could potentially be produced very cheaply—silicone is a low-cost material, while zinc oxide is already produced in large quantities for use in sunscreen.
Another team working on stretchable, health-monitoring patches is based at Northwestern University in Illinois. Researchers there have developed electronic patches that can capture, store and analyse sweat to measure a person's response to exercise. The device collects sweat through tiny channels in the patches. The sweat ends up in small compartments where it reacts to various chemical mixtures, resulting in colour changes. Bring a smartphone near the patch, and the wireless elctrinonics in it trigger an app to take a photo of the device, which it then analyses. The patch can be used to measure the biomarkers of athletes—telling them if they need to drink more water, for instance. In the future, it could potentially be used to detect a range of other biomarkers in order to diagnose disease.
Meanwhile, an international team including scientists from the Thin Film Coatings Group at the University of South Australia is researching ways to deposit electrically-conducting polymers onto hydrogel contact lenses, with some brain-boggling possible applications. An electrical sensor built into your contacts could monitor your glucose levels, for example. And, instead of viewing images on a computer screen, you may one day be able to generate them straight onto your contact lenses.
With a few more years and even, perhaps, a few happy accidental discoveries, what sounds like science fiction may not be as out-there as we think. Electronics that echo and imitate the natural world by bending, stretching and flexing make sense as technology becomes more integrated into our lives, our environments, and even our bodies.